The best way to protect your Gammill “M” style hook is thru daily attention to few key maintenance items.
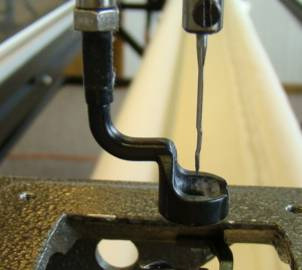
The best way to protect your Gammill “M” style hook is thru daily attention to few key maintenance items:
1. Remove lint and dirt from the entire hook box.
2. Pay special attention to the race areas (Photo A) of the hook (Photo B) to remove any impacted thread lint from the rotating parts.
3. Oil the hook regularly – a drop of oil in the 7:00 to 8:00 position of the hook when the needle is fully up or down will help the hook run cool and quite.
4. Be sure the needle plate is positioned such that the needle is centered in the hole of the needle plate.
5. Position the needle with the scarf (Photo C) to the back or aimed slightly to the right. Never position the needle to the left for this will cause the scarf face to be closed to the approaching hook tip which increases the likelihood of impact to the side of the needle.
6. Change the needle sooner than later. The needle is much easier to change and costs much less than a hook.
7. If you break a needle, immediately check for proper position of the hook tip.
Gammill does not recommend polishing your “M” style hook and this practice may actually cause damage to the hook tip.
Gammill’s “M” style hook is made from extremely hard stainless steel. The hook, properly installed in a correctly adjusted and timed machine will not require any field modifications, and with proper cleaning and oiling techniques will last through years of trouble-free operation. Attempting any field polishing may invite premature wear and destruction of the hook assembly. Without practice and proper materials, the average operator will lack the skill necessary to avoid removing the hardened surface of the hook tip. This will lead to rapid development of a burr that may not have been there before. Access to proper polishing materials is difficult.
In addition, the use of an abrasive offers a potential to deliver some of the abrasive material into the inner race of the hook. This will cause very rapid and catastrophic wear to the inner bearing surfaces of the hook. In short order, the race of the bearing will be worn away causing noise, heat, waffling of the hook tip with relation to the scarf of the needle, deteriorating stitch quality, and finally failure of the hook assembly.
If you do find that a burr has developed on the hook tip, make plans to replace it. Once replaced if you choose to practice polishing your “spare” you won’t have to worry about the rapid deterioration of the operating hook and you have a temporary solution on hand.